Medical devices refer to instruments, equipment, appliances, in vitro diagnostic reagents and calibrators, materials and other similar or related items used directly or indirectly on the human body, including the required computer software. At present, the most common are reusable and disposable equipment. Many equipment are difficult to clean and disinfect thoroughly due to structural reasons, so reusable equipment can easily lead to cross infection. Therefore, whether it is reusable or disposable equipment, to reduce its infection risk, the cleanliness of the environment should be controlled from the source of production.
Disinfection of equipment production workshops is a key step to ensure product quality and patient health and safety. By dividing clear disinfection areas, using special disinfection equipment, using disinfection materials reasonably, standardizing operating procedures, and improving personnel training systems, the sanitation of the production workshop can be effectively ensured. Only by strictly following the hygiene standards can patients be provided with safe and reliable medical products.
In order to reduce the risk of microbial contamination in the production environment of medical devices, it is necessary to strengthen environmental cleanliness control from the source of production. Therefore, some effective measures are needed.
No.1
Clearly defined disinfection areas
If there is a sterile workshop requirement, a special sterilization area should be divided according to the sterility requirements to ensure that the sterilization operation is carried out in an orderly manner and to avoid cross contamination. This area should have a clear boundary with other areas, and staff need to be properly disinfected when entering and leaving.
No.2
Use specialized disinfection equipment
Use specially designed disinfection equipment, such as the YE-5F hydrogen peroxide compound factor disinfector, which can effectively disinfect germs, purify the air, and disinfect the surface of objects. The equipment has multiple disinfection methods and can fully clean the production environment.
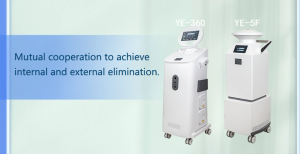
No.3
Reasonable use of disinfection materials
Choose appropriate disinfectants and disinfection methods according to the different production environments and the characteristics of the objects to be disinfected. At the same time, pay attention to the concentration, use method and treatment time of the disinfectant to ensure that the disinfection effect meets the standard.
No.4
Standardized operation procedures
Establish standard operation procedures and operation specifications to ensure that each link meets the hygiene requirements. From receiving raw materials to production and processing to finished product packaging, there is a need for clear operation guidelines and records to track and trace the hygiene conditions of each link.
No.5
Improve the personnel training system
Periodically conduct hygiene training for production workshop staff to make them understand the correct disinfection operation procedures and hygiene specifications. They should master the correct use of disinfectants, operation skills and emergency treatment measures to ensure the efficiency and safety of disinfection work.
Through the above measures, the risk of microbial contamination in the production environment of medical devices can be effectively reduced, and the quality of medical device products and the health and safety of patients can be guaranteed. In the production process of medical devices, always putting hygiene and environmental management first is an important guarantee to ensure product quality and patient safety.
Disinfection of equipment production workshops is a critical step to ensure product quality and patient health and safety. During the production process, cross-contamination can be effectively prevented by dividing clear disinfection areas. At the same time, the use of specialized disinfection equipment and rational use of disinfection materials can significantly improve the disinfection effect. Standardized operating procedures are the basis for ensuring that each step can achieve the expected disinfection effect. Any neglect of details may bring the risk of microbial contamination.
In addition, a sound personnel training system is also key. Only through continuous training and assessment can we ensure that employees are familiar with and strictly comply with health regulations. In order to further reduce the risk of microbial contamination in the medical device production environment, it is necessary to strengthen environmental cleanliness control from the production source. This includes regular air and surface microbiological monitoring of workshops to ensure the environment meets relevant standards.
Effective measures also include using high-efficiency air filtration systems, controlling the temperature and humidity of the production environment, and strictly managing the entry and exit of personnel and materials. All these measures work together to build a clean production environment that meets GMP (Good Manufacturing Practice) requirements. Only by strictly following these health regulations can we provide patients with safe and reliable medical products and ensure their health and safety.
In short, disinfection and environmental control in equipment production workshops are not only part of the production process, but also the basis for ensuring product quality and patient health and safety. Through the comprehensive use of various disinfection and control measures, microbial contamination can be effectively reduced, product safety and reliability can be improved, and patients' needs for high-quality medical devices can be met.